Home
Learn
Trending Topics
Introducing VMS™ Batch Milking
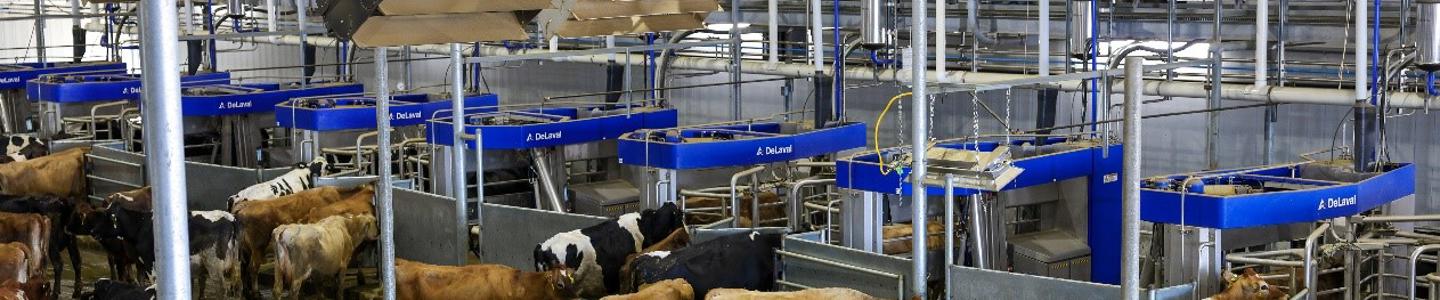
Introducing VMS™ Batch Milking
For more than 20 years, DeLaval VMS™ units have been used on dairy farms across North America and beyond. Some producers utilizing robotic milking facilities have experienced a range of advantages, including reduced labor requirements, more flexibility on and off the farm, valuable cow data, higher production levels, improved milk quality and better cow health.
The key benefit of robotic milking lies in the autonomy it provides to cows, allowing them to decide when to begin the milking process. This choice can be facilitated through a guided cow traffic system or within a free-traffic barn, where cows have the freedom to move about at their discretion. In these setups, dairy cows can express their genetic potential around the clock, meaning they can be milked as often as they like and as permitted by their owner.
What is VMS Batch Milking?
VMS™ Batch Milking is a new way of milking larger groups of cows robotically, and it is gaining traction with currently 13 installations in 10 countries.
In a typical VMS barn, cows are housed in different groups according to their needs, potential and the configuration of the barn. They eat, drink, milk and rest all under the same roof—and on their own schedules over a 24-hour period. Interestingly, farms accustomed to conventional parlor or rotary milking can still reap similar benefits with VMS Batch Milking. Here, the milking process is automated but the familiar routines of milking a herd in a parlor remain under the schedule of the owner.
How does it work?
VMS Batch Milking requires herds to be divided into groups. A person then brings those groups one at a time to the milking center, like parlor milking. One popular barn layout with batch milking involves two rows of multiple VMS units. The facility arrangement mimics a parallel parlor, featuring a central holding area between the robots. Upon milking completion, all cows exit out of the robot to the right and follow the exit lane around the perimeter of the milking center until they are met by a selection gate. This gate can guide them to a herd health sort area, the holding pen or back to their original pen—with no labor involved.
“VMS Batch Milking allows farmers to milk their cows in groups according to lactation stage, like they would in their conventional milking operation,” said Stephanie Dillon, advisory specialist at DeLaval. “Transitioning to batch milking can be seamless for producers since many of the same routines are the same as conventional milking and the requirements for training staff are minimal.”
VMS Batch Milking offers the additional advantage of enabling farms to maintain their total mixed ration (TMR) feeding regimen, avoiding the need to shift to a partial mixed ration (PMR), as the pellets fed in the robot are minimal and used as an incentive or a distraction rather than for nutrition. This approach allows the farm to extract greater value from the home-grown forages they produce. Much like feeding practices, various routines typical in conventional milking operations can remain unchanged in VMS Batch Milking. These include tasks such as cleaning stalls while cows are milking, sorting cows to a designated area for herd management and adhering to set milking times. This continuity helps make the transition to robotics easier for farm personnel, as the learning curve is notably less steep in this style of robotic milking.
Case study: Rancho Pepper Dairy
Rancho Pepper Dairy is the first farm in the U.S. to utilize VMS Batch Milking. In 2022, the organic producer installed 22 DeLaval VMS V300 units to batch milk 2,000 cows at its dairy in Dublin, Texas.
“Rancho Pepper chose VMS Batch Milking for the individual cow data captured by DeLaval VMS and the fewer labor requirements needed to milk the same number of cows as with a traditional parlor,” explained Jason French, VMS solution manager. “The ability to see how each cow is performing and make decisions based on those metrics has also helped them reduce the time needed to manage their herd.”
Dawn Dial, dairy manager at Rancho Pepper Dairy, described the batch milking system as “…a parallel barn with VMS [units] and feed off both sides. You have the VMS doing the job of the people, and it’s working. Through the exit area going back to the corrals is sort gates also, so no matter when she leaves the parlor she goes back to the same pen she came from.” Dawn continued, “These cows are very relaxed, and I feel that they are more relaxed than any parallel [parlor] I have ever seen in my life. I would definitely do this again.”
Conclusion
With the rising cost and limited supply of labor, dairies will continue to explore the benefits of milking robotics. VMS Batch Milking offers clear advantages by removing the labor needed to attach cups to a cow—all while consistently milking her, promoting good udder health and supplying actionable cow data for the herd manager. Farm staff working with cows in the barn can support the robots and respond to and manage any notifications from the robot, keeping the robots working more efficiently.
The popularity of VMS Batch Milking has expanded to more than 10 countries currently working with the system. DeLaval is confident the concept of VMS Batch Milking will continue to flourish as more farmers look to combine the benefits of milking robots with a management style they know and have relied on for years.
Learn more about VMS Batch Milking by registering for the webinar series.